
6月1日,深蓝S7第十万辆量产车在深蓝南京智慧工厂正式下线。自去年6月30日开启交付以来, 实现了35天交付破万辆、5个月交付达到5万辆、不到一年10万辆量产车下线。

深蓝S7凭借超级增程技术、高颜值、高配置等品质,不仅在国内市场销量优异,在国外市场也表现强劲, DEEPAL S07(海外版深蓝S7)自去年底进入泰国市场以来,已跻身当地汽车品牌第一梯队,还成功登顶泰国4月份全品牌纯电动车型销量排行榜首位,展现出强劲的市场竞争力和品牌影响力。
作为一款大五座SUV,深蓝S7车身外观优雅动感,拥有接近0.618黄金分割比例的轴长比;内饰座舱豪华舒适,拥有前排双零重力按摩座椅、双层隔音玻璃等配置;轴距为2900mm,前后排都能享受到宽敞舒适的乘坐体验。此外,深蓝S7所搭载的智能驾驶系统,如自动泊车、360全景影像、透明底盘、车道保持保持功能,减少了用户的驾驶负担,既实用又安全。

依托于深蓝超级增程技术,深蓝S7拥有最高200km(CLTC)的纯电续航里程,馈电状态下拥有4.95L/100km(CLTC)的油耗表现。城市通勤用纯电,长途出行有增程,解决了用户对纯电动车型里程焦虑与补能不便等各种问题。
驾驶操控方面,深蓝S7拥有纯电驱动,天生后驱特质,让驾控体验更优秀;安全方面,深蓝S7搭载同级领先的iBC数字电池管家系统,通过24小时电池全方位监控,10毫秒极速报警,安全预警准确率≥99%,还可实现电池不起火、不冒烟、零热失控。
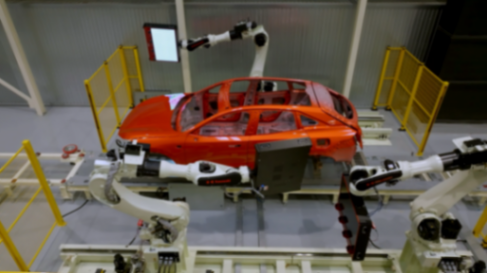
南京智慧工厂共有冲压车间、车身车间、涂装车间、总装车间、电池车间五大车间。冲压车间的自动化率达95%,柔性检测设备速度高达每分钟180万次,3分钟就能完成一个零部件的扫描,扫描精度达0.025毫米,相当于头发丝的五分之一,确保每个零件的每个曲面都完美,整条生产线更拥有5600吨的冲压能力,每2秒就能制造出一个零部件,真正实现了高效生产。
焊接车间实现了真正的智能化和自动化生产。深蓝S7整车有3000多个焊接点位,每一个焊点都进行100%的检测,车身材料不仅采用高强度钢,先进的机器人焊接技术也确保了焊接质量和强度。
总装车间,底盘电池一体化合装工位采用先进的底盘前后桥、电池一体式合装技术。在这里诞生的每一辆深蓝S7,从零部件原材料到整车交付都有11道严格的质量墙管控,确保每一辆深蓝S7都能达到100%的质量监测追溯。

第十万辆量产车的下线,标志着深蓝S7的又一个里程碑,也是其迈向全新征程的新起点。后续,深蓝S07将成为首款搭载华为智驾的深蓝车型,进一步提升智能驾驶能力,拓展智能电动出行的边界。